Electrical cables are vital components in our modern Electrical and Electronics Engineering infrastructure. They facilitate power and data transmission. Tests are carried out on electrical cables to ensure their quality, durability, and safety. These tests evaluate various parameters such as conductor resistance, insulation thickness, overall diameter, and other physical properties of cables. This article by Electrical and Electronics Engineering will delve into the different types of tests conducted on electrical cables, categorizing them as type, acceptance, and routine tests. From the persulphate test to high voltage and insulation resistance tests, we will explore the procedures and significance of each test, shedding light on the meticulous evaluation process that ensures the quality and reliability of electrical power cables.
The methods and types of tests shared here provide a general overview of different testing methods and techniques used in cable testing. While practically dealing with cables, always follow the relevant industrial IEC, IEEE, IS, ICEA, BS, or applicable standards for the specific type of cable you are dealing with.
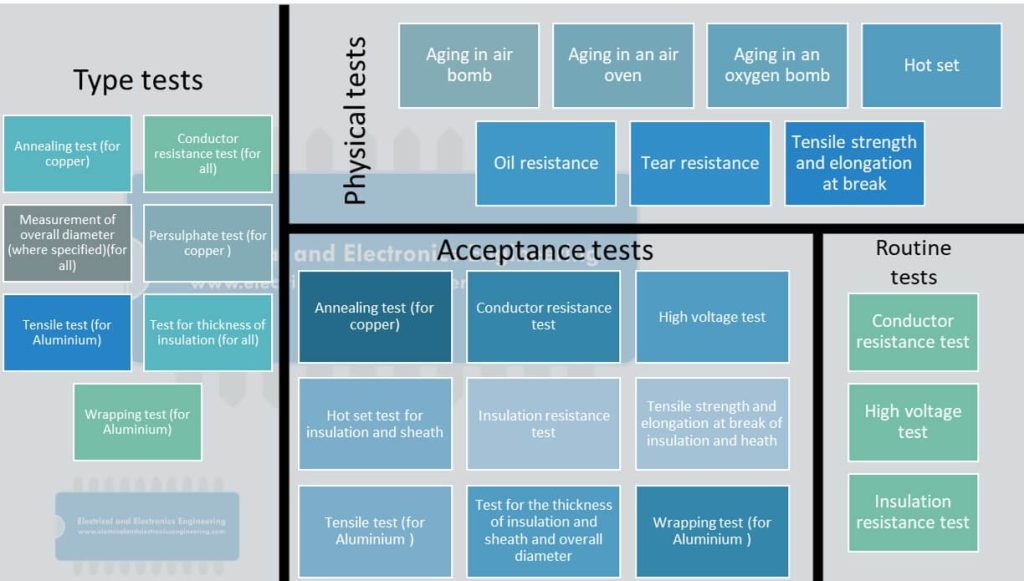
Pre Energization Tests
Before energizing electrical cables, it is crucial to perform thorough pre-energization tests to ensure the cables’ integrity and compliance with project specifications. This involves comparing cable data with drawings and specifications, checking for material damage, and verifying electrical connections to prevent potential hazards and ensure proper functioning.
Comparing Cable Data and Specifications
During pre-energization tests, comparing the cable data with the project drawings and specifications is essential. The process involves checking the number of cable sets, cable size, routing, and insulation ratings. Any discrepancies between the actual cables and the project specifications must be noted on the test sheet to address them promptly.
Inspecting Cable Jacket and Insulation
The uncovered parts of the cables should be carefully inspected for material damage. This inspection also includes assessing the condition of the cable jacket and insulation for exposed sections. The examination must ensure the connection points align with the project’s single-line diagram to guarantee proper installation.
Testing Bolted Electrical Connections
High resistance in bolted electrical connections can lead to inefficient performance and potential hazards. Therefore, a calibrated torque wrench, low-resistance ohmmeter, or thermographic survey should be used to check bolted electrical connections. ANSI/NETA Table 100.12 US Standard Fasteners, Bolt Torque Values for Electrical Connections should be referenced when using a calibrated torque wrench. Any bolted connection value that shifts by more than fifty percent of the smallest value should be investigated when utilizing a low-resistance ohmmeter. Also see: ElectricalandElectronicsEngineering.com article post on USB-C Cable testing.
Visual Inspection of Low Voltage Wire and Cable
Visual inspection is crucial for low-voltage wires and cables. It ensures integrity and proper functioning of cables. During the inspection, the exposed cable jacket and insulation should be carefully examined to detect any signs of damage or wear that could impact performance or safety later on.
Inspecting Compression-Applied Connections
Compression-applied connections play a critical role in cable installations. During the pre-energization tests, it is essential to verify that the connector is appropriately rated for the installed cable size and has the proper indentations to ensure a secure and reliable connection.
Insulation-Resistance Test
Each conductor must undergo an insulation-resistance test with the ground and adjacent conductors. The test should last for one minute using a voltage specified by the manufacturer. If no literature from the manufacturer is available, 500 volts dc should be applied for 300-volt rated cable and 1000 volts dc for 600-volt rated cable. Insulation-resistance values should meet or exceed the manufacturer’s published data or other standard/specification applicable. If the manufacturer data or any other specification recommendation is unavailable, the values should be no less than 100 megohms to ensure cable integrity and safety.
Continuity Tests for Correct Cable Connection and Phasing
Continuity tests are carried out on cables to ensure correct cable connections and phasing. These tests individually confirm each cable’s continuity and verify the uniform resistance of parallel conductors using a low-resistance ohmmeter. Deviations in resistance between parallel conductors must be thoroughly investigated and addressed.
Additional Pre-Energization Tests
In addition to the previously mentioned tests, it is crucial to conduct further pre-energization tests to ensure a comprehensive cable assessment. These additional tests may include but are not limited to, tests for cable capacitance, dielectric loss, and cable impedance to evaluate cable performance thoroughly before energization.
Megger Test for High Voltage Cables
For high-voltage cables, a megger test should be performed. This test involves applying a high DC voltage to assess the insulation quality. The Megger test helps identify potential weaknesses or damage in the insulation that could lead to breakdowns or electrical failures.
Load Bank Testing for Cable Systems
Load bank testing is necessary for cable systems to simulate real-world conditions and ensure their performance under various loads. This test evaluates the cables’ ability to carry the intended electrical load without overheating or exceeding their capacity, providing the reliability and safety of the electrical system.
Type Tests
Type tests are conducted on electrical cables to evaluate their compliance with industry standards and specifications. Type tests are a short name for Prototypes. It includes predominately destructive tests carried out to determine if the cable construction and materials comply with the standard specifications. These tests assess various aspects of cables, including conductor material, insulation thickness, mechanical strength, and electrical performance. Type tests on cables are further classified into five categories:
- Conductor type tests
- Insulation dimension and thickness test
- Insulation physical tests
- Sheath physical tests
- Finished cable tests
Let’s delve into each of these one by one
Type Tests carried out on conductors
Annealing Test (for Copper)
Procedure
- The copper conductor sample is subjected to a specific annealing process
- The sample is heated to a predetermined temperature and then cooled down slowly
Significance: Assesses the mechanical properties and flexibility of copper conductors
Conductor Resistance Test (for all):
Procedure: The resistance of the conductor is measured using an ohmmeter or similar equipment.
Significance: Verifies the conductivity and integrity of the conductor material.
Persulphate Test (Applicable to Tinned Copper Conductor Cable)
The Persulphate Test for copper is a specific test used to determine the purity and conductivity of copper conductors. It is a well-known test carried out on copper materials, including copper wires and cables. The test is typically performed according to the guidelines specified in the relevant industry standards.
Procedure
- The copper conductor sample is immersed in a persulphate solution
- The solution is heated, and the time required for the copper to dissolve is measured
Significance: Determines the purity and conductivity of copper conductors.
Tensile Test (for Aluminum)
Procedure
- An aluminum conductor sample is subjected to tension until it breaks
- The force applied and elongation are measured
Significance: Determines the tensile strength and ductility of aluminum conductors
Wrapping Test (for Aluminum)
Procedure
- The aluminum conductor sample is wrapped around a mandrel of a specific diameter
- The sample is examined for any signs of cracks or fractures in the wrapping
Significance: Evaluates the wrapping and bending properties of aluminum conductors
Type tests for Insulation and Dimensions
Test for Thickness of Insulation (for all):
Procedure
- The insulation thickness is measured at multiple points along the cable using calipers or a suitable measuring instrument
Significance: Ensures the insulation meets the required thickness specifications for electrical safety
Measurement of Overall Diameter (where specified) (for all):
Procedure
- The outer diameter of the cable is measured at various points using a micrometer or similar measuring device.
Significance: Determines if the cable meets the specified dimensions for proper installation and compatibility
Physical Type Tests for Insulation and Sheath
Physical tests for insulation and sheath evaluate the mechanical properties and resistance of the cable’s outer layers of insulation and sheat. These tests help ensure the durability and longevity of insulation and sheath used for electrical cables in various environmental conditions. The following physical examinations are performed:
Aging in Air Oven
Procedure
- A sample of the insulation or sheath material is exposed to elevated temperatures in an air oven for a specified duration.
- The sample is then examined for any signs of degradation or physical changes.
Significance: Simulates long-term exposure to high temperatures and evaluates the material’s resistance to aging.
Aging in Air Bomb – Cable Tensile Testing
Procedure
- A sample of the insulation or sheath material is placed in a sealed bomb and exposed to elevated temperatures and pressure.
- The sample is then examined for any signs of deterioration or physical changes.
Significance: Simulates extreme environmental conditions and assesses the material’s resistance to aging under pressure.
Aging in Oxygen Bomb
Procedure
- A sample of the insulation or sheath material is placed in a sealed bomb and exposed to elevated temperatures and pure oxygen.
- The sample is then examined for any signs of degradation or physical changes.
Significance: Tests the material’s resistance to oxidation and degradation in the presence of oxygen.
Cold bend test
The Cold Bend Test is conducted to assess the ability of a cable to withstand bending at low temperatures. Cables can experience different temperature environments during their service life, and it is crucial to ensure that they maintain their flexibility and mechanical integrity even in cold conditions. The test is particularly relevant for cables used in cold climates or applications where they might be subjected to sub-zero temperatures.
Procedure
- A sample of the cable is conditioned at a specified low temperature, usually between -20°C to -40°C (-4°F to -40°F) for a specific period to ensure the cable is uniformly cold.
- After conditioning, the cable is bent around a specified mandrel diameter (typically, the diameter is determined based on the cable’s diameter)
- The cable is bent to the required angle and held in that position for a specific duration.
- After the bending period, the cable is examined for any visible damage, such as cracks, splits, or separation of insulation or sheath.
- The test results determine the cable’s ability to withstand bending stresses at low temperatures, and it helps assess whether the cable is suitable for use in cold environments.
Cold impact test
The Cold Impact Test is performed to evaluate a cable’s ability to withstand mechanical shocks or impacts at low temperatures. In some cases, cables can be exposed to impacts or sudden stresses even in extremely cold conditions. Therefore, it is essential to ensure the cable’s construction and materials can withstand such extreme conditions without experiencing damage or loss of functionality.
Procedure
- A conditioned sample of the cable is placed in a low-temperature environment, usually at the same temperatures as the Cold Bend Test
- The cable sample is then subjected to a specific level of impact force, either by dropping a weight on the cable or using an impact-testing machine with a controlled impact force
- After the impact, the line is visually inspected for any visible damage, and its electrical performance might also be assessed
Flammability Test (only for SE-3, SE-4):
Procedure
- A sample of the cable is exposed to a flame for a specified duration
- The flame propagation, burning rate, and afterglow time are measured
Significance: Determines the cable’s resistance to flame propagation and its fire safety properties.
Flexing Test on Cables
Flexing tests evaluate the performance of multicore flexible cables that experience frequent bending in their applications. The test ensures the cable operates correctly under rated current and voltage, without any occurrence of short or open circuits. The process involves subjecting the cable to 30,000 cycles of movement using pulley carriers while loaded with test weights and supplied with the rated current and voltage. Monitoring equipment is utilized to detect potential open circuits and short circuits between conductors or between the conductors and the test frame during the test. This assessment ensures the reliability and safety of the flexible cables under real-world conditions.
Gas emission testing determining the halogen acid gas content BS EN 60754-1
The Halogen Acid Gas Test is a crucial evaluation method used to determine the amount of halogen acid gases generated when cable insulation and sheathing compounds are exposed to combustion. This test is applicable to both electrical cables and fiber optic cables, ensuring the safety compliance of these cables.
To conduct the Halogen Acid Gas Test, samples of the polymer insulation or sheathing material are carefully prepared. The following steps outline the procedure:
Sample Preparation:
- Approximately 750mg of the insulation or sheathing material is collected.
- The sample is then cut into smaller pieces to facilitate testing.
Conditioning:
The prepared samples are subjected to a controlled environment.
- They are placed in a conditioning chamber set at a temperature of 23°C (73.4°F) and a relative humidity of 50%.
- The samples undergo conditioning for a period of 16 hours to ensure their stability and uniformity before testing.
By following these preparation and conditioning steps, the samples are ready for the subsequent testing phase. This test method allows for accurate measurement and assessment of the halogen acid gases emitted during combustion, providing critical information about the potential environmental impact and safety considerations associated with the cable materials.
Assessing Acidity Levels through pH Measurement BS EN 60754-2
As part of the Gas Emissions Test, the acidity of gases is determined and recorded using pH measurement, following the guidelines outlined in standard IEC 60754. This test method focuses on evaluating the corrosiveness of the gases emitted during combustion by analyzing the properties of an aqueous solution derived from the evolved gases.
Heat shock test
Procedure: The Heat Shock Test for cables evaluates their ability to withstand rapid and extreme temperature changes. A cable sample is conditioned, then subjected to temperature cycling in a thermal chamber, rapidly alternating between high and low temperatures. The cable’s mechanical and electrical properties are examined after a specified number of cycles. This test ensures cables can endure temperature variations without compromising performance, making them suitable for various industries. Proper selection of temperature ranges and dwell times is crucial for an accurate representation of real-world conditions.
Significance: Manufacturers use this test to enhance product design, comply with industry standards, and assure customers of cable reliability.
Hot Set
Procedure: A sample of the insulation or sheath material is subjected to a specified temperature for a specific duration.
- The sample is then stretched to a predetermined length and cooled down
- The material’s ability to retain its shape is evaluated
Significance: Assesses the material’s resistance to deformation and its ability to recover its original shape after exposure to heat.
Hot deformation test
The Hot Deformation Test evaluates a cable’s ability to maintain its structural integrity and shape under high-temperature conditions. A cable sample is heated to a specified temperature, and any deformation or distortion is observed. This test ensures cables can withstand heat without significant changes to their physical form, vital in applications with elevated operating temperatures.
Loss of mass test
The Loss of Mass Test assesses a cable’s resistance to material degradation when exposed to extreme heat. The cable sample is subjected to high temperatures, and any weight loss due to material decomposition or evaporation is measured. This test helps determine cable durability and suitability for environments with potential heat-related material deterioration.
Mass of zinc coating for galvanized wire armor
The test for the mass of zinc coating on galvanized wire armor is conducted to determine the amount of zinc present on the surface of the wire. This test ensures that the wire armor meets the required standards for corrosion resistance and durability. The wire armor sample is carefully weighed before and after stripping off the zinc coating. The difference in weight provides the mass of the zinc coating, which is then compared to the specified requirements. By verifying the mass of the zinc coating, this test guarantees the effectiveness of the galvanization process in protecting the wire against corrosion and extends its service life.
Oil Resistance
Procedure
- The insulation or sheath material is immersed in a specified type of oil for a defined period
- The material’s physical properties and resistance to oil absorption or deterioration are assessed
Significance: Determines the material’s ability to withstand exposure to oils commonly found in various industrial applications.
Oxygen index test
The Oxygen Index Test assesses a cable’s flammability by determining the minimum concentration of oxygen required for it to sustain combustion. The cable sample is exposed to a controlled oxygen-nitrogen mixture, and the oxygen percentage at which the cable starts burning continuously is measured. A higher oxygen index indicates a cable’s greater resistance to flames, making it more suitable for applications where fire safety is crucial, such as in buildings, transportation, and industrial settings. This test helps manufacturers ensure their cables meet safety standards and comply with fire resistance requirements in various industries.
Tensile Strength and Elongation at Break
Procedure
- A sample of the insulation or sheath material is subjected to tension until it breaks
- The maximum force applied and the elongation at the break are measured
Significance: Determines the material’s ability to withstand stretching and resist deformation.
Tear Resistance
Procedure
- A sample of the insulation or sheath material is subjected to a tear force until it rips
- The maximum force required to tear the material is measured
Significance: Evaluates the material’s resistance to tearing or punctures.
Test for Temperature Index
The Temperature Index Test determines the maximum continuous operating temperature for an electrical cable. It involves exposing the cable to increasing temperatures, measuring critical properties like elongation and tensile strength, and calculating the temperature index. This index indicates the temperature at which the cable can safely operate long-term without significant mechanical property degradation.
Test for Halogen Acid Gas Evaluation
This test assesses the amount of halogen acid gases emitted by a cable when exposed to high temperatures. The test is crucial for applications where cable combustion can release toxic gases. It helps evaluate the fire safety and environmental impact of the cable’s materials in case of fire.
Thermal Stability Test
The Thermal Stability Test analyzes a cable’s ability to withstand elevated temperatures over time without significant deterioration. The cable is exposed to a constant high temperature for an extended period, and changes in its mechanical and electrical properties are measured. This test ensures the cable’s reliability in applications with prolonged exposure to elevated temperatures.
Smoke Density Testing for Cables
Smoke Density Testing for Cables is a critical evaluation method that aims to measure the amount of smoke produced during the combustion of cables. This test, also referred to as the 3-metre cube test, follows the guidelines specified in BSEN 61034 (formerly known as BS EN 50268).
The primary objective of this test is to determine the volume of smoke generated when cables are burned. By quantifying the smoke density, the test provides valuable information about the potential visibility impairment and toxicity hazards that may arise in the event of a fire involving cables.
During the test, a three-dimensional cube with a volume of three cubic meters is used as a controlled environment. The cable sample is carefully burned within this cube, and the resulting smoke is observed, measured, and analyzed. The measurement is typically conducted using specialized equipment that can accurately assess the density of smoke produced.
The smoke density is quantified by evaluating the obscuration level caused by the smoke within the three-meter cube. This measurement allows for a comparison against specified requirements and industry standards. It helps determine the suitability of the cable materials and their compliance with regulations regarding smoke emissions in various applications, such as buildings, transportation, and industrial settings.
By performing smoke density testing, cable manufacturers and regulators can assess the potential impact of cable combustion on human safety, evacuation procedures, and visibility in critical situations. It aids in the selection of cables with lower smoke emissions, contributing to enhanced fire safety and improved emergency response measures.
In conclusion, Smoke Density Testing for Cables, also known as the 3-metre cube test, is a standardized method used to determine the volume of smoke produced during cable combustion. By evaluating the smoke density, this test provides crucial insights into visibility impairment and potential toxicity hazards during fires. It plays a significant role in ensuring compliance with safety regulations and enables the selection of cables with lower smoke emissions, ultimately enhancing fire safety measures.
Vertical Flame Testing for Cables
Vertical Flame Testing for Cables is a fundamental evaluation method aimed at assessing the flame retardant properties of a single cable length. This test follows the guidelines specified in BSEN 60331-1-2, which focuses on evaluating the cable’s resistance to fire propagation
During the test, a vertically oriented cable sample is subjected to a controlled flame source. The flame is applied to the bottom end of the cable, and its behavior and ability to resist flame propagation are carefully observed and measured. Parameters such as flame spread rate, burning duration, and dripping behavior are assessed.
By performing the Vertical Flame Test, it is possible to evaluate the cable’s ability to self-extinguish and prevent the fire from spreading further along its length. This information is vital in determining the cable’s compliance with fire safety regulations and standards. It aids in selecting cables that have adequate flame retardant properties for applications where fire hazards are a concern, such as buildings, industrial facilities, and transportation systems.
Shrinkage Tests for Cable Insulation
Cable testing for shrinkage is a crucial evaluation method designed to assess the behavior of insulation materials under service conditions. The purpose of this test is to determine whether the insulation material will shrink back when subjected to stresses encountered during cable operation. It is essential to prevent any shrinkage, as it can pose significant dangers by exposing live conductors, potentially leading to electric shock or short circuits.
Shrinkage in cable insulation can occur due to various factors, such as the inherent stresses in the manufacturing process or handling during subsequent stages. To ensure the reliability and safety of cables, the test for shrinkage of cable insulation is specified in the standard BS EN 60811-502. This standard provides accredited test methods for evaluating the behavior of non-metallic materials used in different types of cables.
Water Absorption Test (for Insulation):
Procedure
- A sample of the insulation material is immersed in water for a specific duration
- The sample is then weighed before and after immersion to measure the water absorption
Significance: Assesses the insulation material’s water resistance and its ability to maintain electrical properties when exposed to moisture.
Physical type tests for sheath
Ageing in Air Oven
In this test, the cable sample undergoes prolonged exposure to elevated temperatures in an air oven. It assesses the cable’s aging characteristics and performance when subjected to heat and air, helping determine its suitability for long-term use.
Heat Shock Test
The cable is rapidly subjected to extreme temperature cycling between high and low levels. This evaluates the cable’s ability to withstand thermal stress, ensuring it can endure temperature fluctuations without damage.
Hot Deformation
The cable sample is exposed to high temperatures to analyze its deformation behavior. This test assesses the cable’s ability to maintain shape and mechanical integrity under elevated temperatures.
Loss of Mass Test
The cable is heated to measure any weight loss. This test evaluates the cable’s resistance to thermal decomposition and potential material volatilization under heat exposure.
Oxygen Index Test
The cable’s combustion resistance is measured by determining the minimum oxygen concentration needed for sustained burning. This test provides vital fire safety information for cable applications.
Shrinkage Test
The cable sample is heated, and any dimensional changes, such as shrinkage, are measured. This test evaluates the cable’s response to temperature variations and ensures dimensional stability under heat.
Tensile Strength and Elongation at Break
The cable sample is subjected to tension until it breaks, measuring its strength and elongation capability. This test determines the cable’s mechanical performance and its ability to withstand stretching forces.
Test for Halogen Acid Gas Evaluation
The cable is exposed to high temperatures, and the emitted halogen acid gases are evaluated. This test ensures the cable’s compliance with safety standards and assesses its environmental impact during combustion.
Test for Smoke Density
The cable sample is burned, and the smoke density is measured. This test assesses the cable’s smoke emission characteristics during fire conditions, providing crucial information for fire safety and evacuation plans.
Test for Temperature Index
The cable undergoes increasing temperature exposure, measuring properties like elongation and tensile strength. The Temperature Index is calculated, determining the cable’s maximum safe operating temperature.
Thermal Stability
The cable sample is exposed to a constant high temperature for an extended period, evaluating any changes in mechanical and electrical properties. This test ensures the cable’s reliability under prolonged elevated temperature exposure.
Test carried out on completed cables
Additional Ageing Test (OU Cables Only)
An extension of standard ageing tests for cables, specifically for cables used in harsh outdoor environments. The OU cables undergo accelerated ageing under conditions of higher temperature, humidity, and UV exposure. This test assesses their durability and performance in outdoor settings, ensuring they can withstand prolonged exposure to environmental factors.
Conductor Resistance/Armor Resistance Test using Micro-ohmmeter with four wire Kelvin bridge principle
The Conductor Resistance/Armor Resistance Test employs a Micro-ohmmeter using the four-wire Kelvin bridge principle. This method accurately measures the resistance of conductors and armor in electrical cables. The four-wire Kelvin Bridge eliminates lead resistance, providing precise readings. This test ensures proper functioning and safety of the cables by verifying their resistance characteristics.
Flammability Test
Evaluates a cable’s resistance to flame propagation. The cable sample is exposed to a controlled flame, and its reaction to the flame, such as burning rate and self-extinguishing properties, is observed. This test helps identify cables that are less likely to contribute to fire spread and ensures compliance with safety standards.
Flex Test
Determines a cable’s flexibility and ability to withstand repeated bending. The cable sample undergoes multiple bending cycles at various angles and tensions. The test ensures the cable can endure flexing in practical applications without cracking, deforming, or failing.
High Voltage Test
Tests the cable’s insulation integrity under high electrical stress. The cable is subjected to high voltage for a specific duration, checking for any electrical breakdown or flashovers. This test ensures the cable’s insulation can withstand the rated voltage and prevents electrical hazards.
High Voltage Test (Water Immersion Test)
A variation of the high voltage test, where the cable is immersed in water during the test to simulate damp or wet conditions. The test assesses the cable’s ability to maintain electrical insulation properties even when exposed to moisture.
High Voltage Test or Spark Test
A non-destructive test to identify insulation defects and weak points in the cable. The cable’s surface is subjected to a high-frequency, high-voltage spark, and any flashovers or corona discharges indicate potential insulation weaknesses.
Insulation Resistance
Measures the cable’s ability to resist electrical leakage through its insulation. A voltage is applied to the cable, and the resulting current is measured. The test ensures the insulation is free from defects that could lead to electrical leakage or performance degradation.
Long-Term Resistance to DC Test on Cables
This test aims to evaluate the long-term resistance of insulation to a direct current (DC) voltage applied between the conductor and water. The test setup involves a 220V DC power supply and a heated water tank filled with a saline solution. The testing procedure follows the specifications outlined in BS EN 50395. This method ensures the assessment of insulation performance over an extended period to ensure its reliability and suitability for practical applications.
Acceptance Tests
Acceptance tests are conducted to verify the quality and compliance of electrical cables before they are accepted for use. These tests ensure that the cables meet the required specifications and standards. The following tests constitute acceptance tests:
Annealing Test (for Copper)
Procedure: Same as mentioned earlier in the type tests section.
Significance: Confirms the mechanical properties and flexibility of copper conductors.
Conductor Resistance Test
Procedure: Same as mentioned earlier in the type tests section.
Significance: Verifies the conductivity and integrity of the conductor material.
Flammability test
Same as mentioned in previous section.
Tensile Test (for Aluminum)
Procedure: Same as mentioned earlier in the type tests section.
Significance: Validates the tensile strength and ductility of aluminum conductors.
Wrapping Test (for Aluminum)
Procedure: Same as mentioned earlier in the type tests section.
Significance: Ensures the wrapping and bending properties of aluminum conductors.
Test for Thickness of Insulation and Sheath and Overall Diameter
Procedure: Same as mentioned earlier in the type tests section.
Significance: Ensures compliance with specified insulation thickness, sheath thickness, and overall diameter.
Tensile Strength and Elongation at Break of Insulation and Sheath
Procedure: Same as mentioned earlier in the physical tests section.
Significance: Validates the mechanical properties and durability of the insulation and sheath materials.
Halogen acid gas evaluation test
The Halogen Acid Gas Evaluation Test assesses the amount of halogen acid gases emitted when a cable is exposed to high temperatures. When cables burn in fire incidents, certain materials may release halogen gases (e.g., chlorine, fluorine, bromine, iodine) that can form corrosive and toxic compounds, posing a severe threat to life and equipment. This test involves subjecting the cable sample to elevated temperatures in a controlled environment and measuring the emitted gases. By determining the cable’s halogen acid gas properties, manufacturers can ensure compliance with safety standards and select materials with lower halogen content, reducing potential environmental and health hazards in fire scenarios.
Hot Set Test for Insulation and Sheath
Procedure: Same as mentioned earlier in the physical tests section.
Significance: Assesses the resistance of insulation and sheath materials to deformation under heat.
High Voltage Test
Procedure: Same as mentioned earlier in the high voltage tests section.
Significance: Verifies the cable’s ability to withstand high voltage stresses without electrical breakdowns.
Insulation Resistance Test
Procedure: Same as mentioned earlier in the physical tests section.
Significance: Validates the quality and integrity of the insulation material.
Persulphate Test (Applicable to Tinned Copper Conductor Cable)
The Persulphate Test is conducted on tinned copper conductor cables to assess their resistance to corrosion. The test involves immersing the tinned copper conductor in a solution containing persulphate, simulating harsh environmental conditions. After a specified duration, any visible signs of corrosion or degradation are examined. This test ensures the tinned copper conductor’s reliability and suitability for applications in corrosive environments, such as marine or industrial settings.
Smoke Density Rating Test
The Smoke Density Rating Test evaluates the amount of smoke emitted by a cable during combustion. The cable sample is burned in a controlled environment, and the generated smoke is measured and analyzed for its density and opacity. This test is essential for assessing fire safety, as it helps identify cables with low smoke emission, enabling better visibility and safer evacuation during fires in confined spaces like buildings, tunnels, or aircraft.
Temperature Index Test
The Temperature Index Test determines the maximum continuous operating temperature for a cable. It involves exposing the cable to increasing temperatures and measuring critical properties like elongation and tensile strength. The temperature index is then calculated, indicating the temperature at which the cable can safely operate long-term without significant mechanical property degradation. This test ensures cables can handle elevated temperatures in their intended applications without compromising performance or safety.
Oxygen Index Test
The Oxygen Index Test evaluates a cable’s fire resistance by measuring the minimum concentration of oxygen required for sustained burning. The cable sample is exposed to controlled conditions of oxygen and heat, and the flame’s propagation is observed. This test provides crucial information about the cable’s flammability and fire safety properties, allowing manufacturers to design cables suitable for environments where fire hazards are a concern.
Routine Tests
Routine tests are essential evaluations performed on cables to ensure their quality, functionality, and compliance with industry standards. These tests are conducted on a regular basis during the manufacturing process to verify the performance and reliability of cables before they are released for use. Let’s explore the significance of some common routine tests conducted on cables:
Conductor Resistance Test
The Conductor Resistance Test measures the electrical resistance of the cable’s conductor. A low-resistance conductor is crucial for efficient power transmission and reduced energy losses. In this test, a known current is passed through the conductor, and the voltage drop is measured. From this, the resistance is calculated using Ohm’s law. The test ensures that the conductor meets the specified resistance requirements and verifies the quality of the conductor material and its cross-sectional area.
High Voltage Test
The High Voltage Test, also known as Dielectric Withstand Test or Hi-Pot Test, evaluates the cable’s insulation integrity and its ability to withstand high voltage stresses without breakdown. A high voltage is applied between the conductor and the cable’s metallic shielding or between multiple conductors. The test is conducted for a specified duration, and the insulation is checked for any disruptive breakdown or flashover. This test helps ensure the cable’s safety, reliability, and compliance with safety standards and regulations.
Concluding Remarks
Electrical cables undergo comprehensive tests to ensure their quality, reliability, and compliance with industry standards. Type, acceptance, and routine tests collectively evaluate various parameters, including conductor material, insulation thickness, mechanical strength, and electrical performance. These meticulous testing procedures ensure that electrical cables meet the required specifications, delivering safe and reliable power transmission. By understanding the different types of tests performed on electrical cables, we can appreciate the thorough evaluation process that guarantees these essential components’ quality, durability, and safety in our modern infrastructure.
References and Further Recommended Readings
- Electrical Power Cable Engineering. (2017). Ukraine: CRC Press.
- Electrical cable. (2023, July 17). In Wikipedia. https://en.wikipedia.org/wiki/Electrical_cable
- VLF cable testing. (2023, May 27). In Wikipedia. https://en.wikipedia.org/wiki/VLF_cable_testing
- WHAT IS CABLE TESTING AND HOW IS CABLE TESTING DONE carelabz article: https://carelabz.com/what-cable-testing-how-cable-testing-done/
- BASEC Electrical tests – https://www.basec.org.uk/testing/electrical-tests/
- Testing of Electrical Power Cable Electrical4u.com article: https://www.electrical4u.com/testing-of-electrical-power-cable/
- Scaddan, B. (2015). PAT: Portable Appliance Testing: In-Service Inspection and Testing of Electrical Equipment. United Kingdom: CRC Press.
- What are electrical cable routine tests? article by Eland Cables: https://www.elandcables.com/the-cable-lab/faqs/faq-what-are-electrical-cable-routine-tests
- Power Cable Testing and Diagnostics Overview guide on Test Guy – https://wiki.testguy.net/t/power-cable-testing-and-diagnostics-overview/79
- Type & Commissioning Testing of High Voltage Cables – https://www.inmr.com/type-commissioning-testing-of-high-voltage-cables/
- Indian Standard CROSSLINKED POLYETHYLENE INSULATED THERMOPLASTIC SHEATHED CABLES — SPECIFICATION – PART 2 FOR WORKING VOLTAGES FROM 3.3 kV UP TO AND INCLUDING 33 kV
- IS 10810 (Electrical Cables and Wires)
- IEC 60840 – INTERNATIONAL STANDARD Power cables with extruded insulation and their accessories for rated voltages above 30 kV